

Photo 3 shows the top of the leadscrew in place I simply extended the ballscrew by drilling and reaming the end 8mm diameter to a depth of 40mm and Supergluing a length of 8mm silver steel into the orifice. So, as shown in Photo 2, it was a simple job to fit one of the motor mounts that DivisionMaster used to sell for converting rotary tables for CNC use to the top of the column, and drill a hole through the top of the casting to allow the leadscrew to be extended up into the mount. The logical conclusion of this decision was to place the motor on top of the Z axis casting rather than at the bottom of the column. I decided that there should be ample torque and mechanical advantage around to dispense with the reduction drive, and opted for direct drive to the leadscrew as with the X and Y axes. A significant part of his decision was to make sure that the Z axis motor wasn't underpowered for the job the 2:1 reduction drive meant that there would be plenty of torque available for this job, which has to contend with the mass of the head and the frictional resistance imposed by the gas strut that is fitted as a counterbalance for the head. With the Z axis, I also adopted a slightly different approach to Dick''s he used a 2:1 toothed belt/pulley reduction drive, mounting the motor at the bottom of the leadscrew. Photo 1: Oldham coupling half in position on X-axis leadscrew I used the clamp type Oldham couplings, and used a little Locktite threadlocker on the threads before adjusting them to their final position. Photo 1 shows one of the threaded coupling halves in place on the X axis. This has the advantage of keeping the leadscrew extension as short as possible, so the motors stick out a little less. I realised that by threading the leadscrew half of the Oldham coupling M12 it could perform two jobs - adjusting the end float and coupling to the motor.
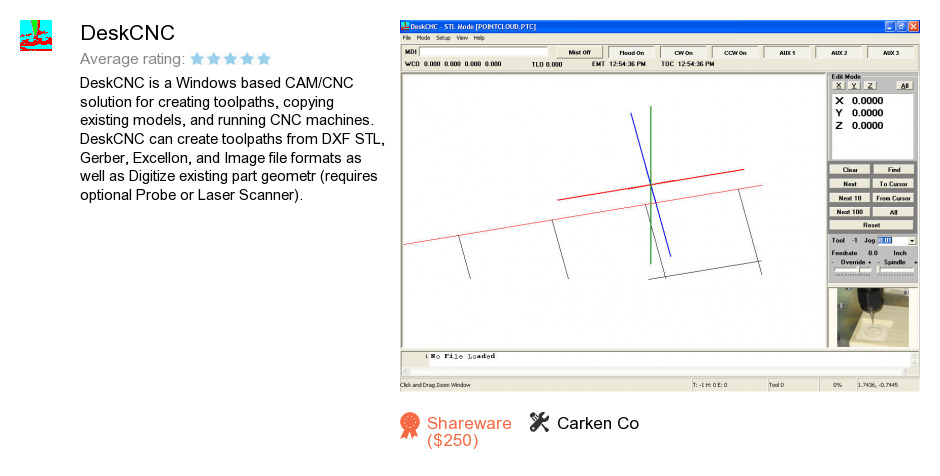
It is necessary to provide end float adjustment for the thrust bearings on these axes. I decided that the X axis nut was just big enough to be machined out to hold a ballnut, which saved a little time and effort. Dick modified the existing bronze Acme feed nut for the Y axis to act as a mount for the ballnut, but replaced the X axis feednut with a new, slightly larger piece of bronze machined to fit in its place. Installing the leadscrews in the X and Y axes proceeded pretty much as Dick described in his articles (MEW December 2004/January 2005). As some of these detailed differences may be of interest to other would-be CNC-ers, I decided to put together a small article to describe them. The overall approach I took was broadly the same as Dick has described - replacing the leadscrews on all axes with 2mm pitch THK ballscrews, using size 23 stepper motors, and so on however, my conversion differs in a number of details from Dick's. Dick kept me updated with his progress as he performed his conversion, knowing that I planned to do a similar conversion in due course, so I not only had the benefit of seeing his articles before attempting my own conversion, but also the benefit of having talked through some of the techniques with him at various times. Introductionĭick Stephen has written extensively in Model Engineers' Workshop magazine of his experiences with CNC conversions, and most recently on converting an X3 mill to CNC. NOTE: Follow the underlined links to find references, figures, other articles etc. Copyright © Tony Jeffree, 12th March 2006.
